
-
President : Looking back on the beginning of the Thai factory in October of 2012, we are hoping to take our company to the next step. I believe we have accomplished our initial goals of building a stable and reliable product supply. Including Thailand, we want to continue breaking into the various Asian markets while continuing to perfect the products and sales while also moving forward with further development of our OEM Type Metalworking Service. I also want to utilize our manager’s, Takayuki Kitayama, background in OEM Service Engineering and his experience of being Quality Control Manager at the head office to continue to better the company.
-
T. Kitayama : With the contributions of my predecessor and growth of the staff in Thailand, the functionality of the current Thai factory has expanded immensely and has established a good reputation as a grease nipple manufacturer. On the other hand, we always question our current position of how self-standing our operations are. With the majority of initial sales directed to the main Japan factory, the quality and product delivery timing was quite flexible between the two factories. Initially the goal of the Thai branch was to have operating machines, and it was the job of the main factory in Japan to cover its shortcomings. That decision, I believe, made all of the difference. However because of that decision, there still are a lot of topics that need to be addressed. We believe that it is necessary to bring those topics to the table and apply the PDCA cycle in order to build up knowledge and experience at the Thai factory.
The development of the OEM Service starts from the acquisition of BOI license. Because of my background in OEM Service Engineering, there are many things that I am still getting used to in such corporate services world. However, because of the amazing environment that allows you to create and make, I feel an immense excitement for the road here on end.
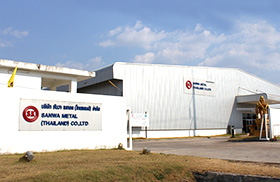
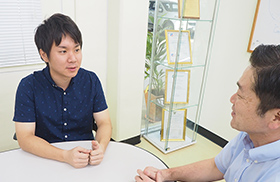
-
President : The experience of building our first overseas factory these past five years was a new challenge and great learning experience. We know you’ve been through a lot during this time and are still working hard to fix the places that are lacking.
-
T. Kitayama : To be honest, there were a lot of challenges and we still have more to face. We believe that the opportunities for growth show themselves at the opportune time and now is our chance to address those issues we had in the beginning. Though however how hard we work, I’m sure I will always ask “What could have I done better?”. Despite these challenges, I am thankful that we have topics to discuss. When I was working in Japan, I was able to focus on my work without much concern for what went on around me. With its long history, the Japan factory offered a fully-developed environment and infrastructure that could function much on its own. While the Thai factory is still small, being the manager of the factory, I’ve come to understand how the different aspects of the organization tie into each other. I find that it is important to repeat the process of finding the weak parts of the company and constantly improving on them. Through these experiences, I’ve learned a great many things.
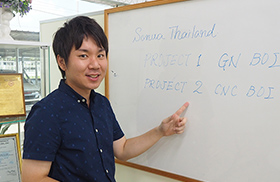
-
President : Because of the various lessons we’ve learned through taking on these challenges, there have been a lot of new things we realized on the Japan side as well. It now seems like the two factories are working together in unison for the future of the company.
-
T. Kitayama : That is why I am here. I want the Japanese factory to one day request us to teach them the knowledge we gained through the development of the Thai factory. If you are a team member here at Sanwa in Japan or in Thailand, my hope is that we can all strive towards a shared goal. I think the first step in doing that is to fully establish the Thai factory’s independence. The Thai factory is still new, and although there are a number of things to solidify, our current state has a lot of advantages. There is a lot of flexibility in the beginning stages. We get a lot of questions from our staff like, why do you do things in this way? How would the Japanese factory solve these issues? After thinking about it all I realized that there were a lot of things that we do because it is natural to us, but we don’t know the reason and we aren’t aware of our actions.
Throughout the years we have acquired patterns in our work and sadly that familiarity can prevent us from asking necessary questions for growth. Once someone in the company has established a habit, it becomes a part of the company and people forget how it came to be. This may only be natural, but in terms of building up organizational knowledge, it remains a challenge for us nonetheless. Because of the hard work and thought everyone is putting into, I believe the Thai factory will someday be able to contribute to the needs of the Japanese factory in the future as well.
-
President : Establishing the OEM service came with a lot of uncertainties. I want to ask for the necessary support of the Japanese factory in the developing process. After all, we are all a part of the same team.
-
T. Kitayama : In the beginning there are a lot of issues to deal with so it is important to have all the help we can get. Some may feel that even if we do ask for support, because of the distance, the level of priority may be of question. So we want even more of the veterans, the main body of staff and the new comers to come and visit the Thai factory and interact with the local area to build connections. We feel that if we can connect both the Japanese and Thai factories together to make a network, it will make communications smoother. For future overseas meetings as well we will utilize online video to make the whole of communication easier. We will soon be able to share the current situations of each factory in real time. To the staff that are currently in Japan — please come to Thailand! We are waiting for you! [laughs]
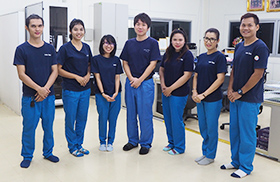
Back to FEATURES top page